烧结配矿之关键所在
发布于 2021-09-06 12:45 ,所属分类:试题库考试资料大全
欢迎加入电炉短流程低碳高质量发展技术交流群
加小编请注明“公司+姓名+工作岗位”
:15373652759/15176109015/18132629730
部分内容摘要
一、四大类铁矿粉的烧结特性
铁矿粉的烧结特性与其密度、颗粒大小、形状及结构、黏结性、湿容量、烧损、软化和熔化温度等因素有关。
介绍磁铁精矿粉的物理特性和烧结性能。
详细阐述赤铁矿粉烧结优于磁铁精矿粉烧结的主要原因:
1)烧结矿矿物结构决定烧结矿质量
2)烧结过程料层透气性是影响烧结矿质量的主要因素
详细阐述褐铁矿的物理特性和多重烧结特性。
因褐铁矿烧结性能中等,价格相对低,非常有利于降低烧结原料成本,近年来将褐铁矿作为烧结重要铁矿粉之一,研究褐铁矿粉高配比低成本烧结具有现实意义。
褐铁矿高配比低成本烧结时,如果因液相量过多而降低转鼓强度和烧结生产率,需增加结构致密且流动性较差的赤铁矿粉和磁铁精矿粉配比。
从结晶水分解吸热的角度考虑,褐铁矿粉烧结需适当增加固体燃耗,保持一定的烧结温度,但从同化性和液相流动性好的角度考虑,褐铁矿粉烧结又需适当降低固体燃耗,最终燃耗如何变化要根据具体配矿和生产实践决定,不能盲目增减燃耗。
烧结温度下,菱铁矿FeCO3首先吸热分解成FeO和CO2气体,因FeO是不稳定相,发生氧化放热反应而生成Fe3O4和Fe2O3,相同条件下菱铁矿烧结比磁铁矿燃耗高,但比赤铁矿燃耗低。因菱铁矿烧损大和分解逸出CO2气体,矿物颗粒不能紧密接触,形成疏松多孔结构的烧结矿。菱铁矿烧结具有水分低、烧结后铁品位提高幅度大、固体燃耗低、转鼓强度低等特点,因烧损大需将粒度控制在6mm以下为宜。
四大类铁矿粉特性比较:
理论铁含量:磁铁矿>赤铁矿>褐铁矿2Fe2O3·3H2O>菱铁矿
理论FeO含量:菱铁矿>磁铁矿>赤铁矿>褐铁矿
理论烧损:菱铁矿>褐铁矿>赤铁矿>磁铁矿
二、提高混匀效果的主要措施
1)有完善的中和混匀系统和科学管理方法并严格执行。
2)原料有足够的安全储量,保证混匀矿连续稳定生产。
3)稳定入厂原料成分,来料按品种和成分分别堆放,标识定置管理,不得混堆。
4)严控入厂原料水分和粒度,不得因水分过大而影响混匀效果,大粒料需经破碎筛分处理后再混匀,避免铺料过程中产生粒度偏析。
5)对于来量少、配比小、成分波动大的多品种循环物料,预先通过质量配料和混匀工艺形成综合粉后再参与混匀矿造堆。
6)混匀矿造大堆,一堆一取交替进行,铺料要匀、薄、层数多,取料要全断面多点垂直切取,避免不均匀取料。
7)设计完善的混匀矿端部料处理工艺,将端部料返回一次料场循环使用。如果没有端部料处理工艺,采取改变布料起点和终点位置的多段布料方式,力求减少端部料量及其成分波动。
8)根据物料品种、水分、粒度、成分不同,合理调整不同原料在混匀矿配料矿槽的布置位置,减小沿混匀矿堆横截面方向上粒度和成分的波动,例如TFe或SiO2含量相差很大的几种物料靠近布置;水分大、粒度粗的物料不宜最后入堆;辅料杂料、炉尘等配比小的物料应堆置在料堆横断面的中部等。
9)选择混匀效率高的取料机,如双斗轮取料机,同时取混匀矿堆的端部和中部料,减小因粒度偏析而造成的成分偏析。
三、生石灰主要特性和作用
生石灰是石灰石经高温煅烧而成的,化学反应方程式为CaCO3=CaO+CO2。
900℃下,CaCO3热分解产生101.325KPa的CO2。实际生产中为加快石灰石的分解,将煅烧温度提高到1000~1100℃,由于石灰石原料粒度不均匀和煅烧温度分布不均匀等原因,产品生石灰常有生烧和过烧现象。
1、生石灰的生烧、灼减、过烧
生石灰的生烧指未分解的石灰石,难溶于水,与水不发生化学反应,当有CO2存在时,发生化合反应CaCO3+CO2+H20=Ca(HCO3)2。
生烧率指未分解的石灰石质量G石灰石占生石灰总质量G生石灰的百分数。
灼减指生石灰被加热到1000℃左右,完全灼烧后失去的质量占生石灰总质量的百分数。生石灰灼减一是由于存在残余未分解的CaCO3,二是由于生石灰吸收了大气中的水分和CO2。因烧结用的生石灰存储在料仓内且用密封罐车输送、压缩空气或氮气打入烧结配料仓,吸收大气中的水分和CO2极少可忽略不计,所以生石灰灼减几乎是残余未分解CaCO3灼烧后放出的CO2量GCO2占生石灰总质量G生石灰的百分数。
由生烧率K=(G石灰石÷G生石灰)×100%,灼减η=(GCO2÷G生石灰)×100%推导出
生烧率K=(G石灰石÷GCO2)灼减η=(100÷44)灼减η=2.273灼减η
(CaCO3分子量为100,CO2分子量为44)
生石灰灼减高,则生烧率高,表明有较多的CaCO3未完全煅烧分解生成CaO,粘结力差。
生石灰的过烧指石灰石煅烧过程中由于局部温度过高,与硅酸盐互相熔融生成的硬块和消化很慢的石灰,短时间内不能被水化。
过烧石灰结构致密气孔率低,表面常包覆一层熔融物,活性度差,水化很慢。
生石灰生烧率和过烧率之和小于15%,能充分发挥提高料温、强化制粒等作用。
2、生石灰的活性度
1)生石灰活性体积检测
CaO+H2O=Ca(OH)2生石灰水化反应式
Ca(OH)2+2HCl=CaCl2+2H2O水化产物与盐酸中和反应式
(1)称取1~5mm生石灰试样50g,放入干燥器中备用。
(2)量取40±1℃水2000ml倒入3000ml烧杯中,开启搅拌器,用温度计测水温。
(3)烧杯中加酚酞指示剂8~10滴,将生石灰试样一次倒入水中消化并开始计时。
(4)消化开始呈红色时用4N的HCl滴定直到红色消失,又出现红色时继续滴入4N的HCl,直到混合液中红色再消失,如此往复操作,记录10min内消耗4N的HCl总毫升数,即为生石灰活性体积。
2)生石灰活性度计算
生石灰活性度=0.112V÷GC=0.112V÷50C
式中0.112——换算系数
V——生石灰活性体积,ml
G——生石灰试样质量,50g
C——生石灰CaO含量,%
生石灰活性度表征一定质量(50g)的生石灰中CaO水化反应后生成Ca(OH)2,在10min内用4N的HCl中和Ca(OH)2所消耗的毫升数,反映生石灰水化反应性能。
3、如何目测判断生石灰CaO含量
观察生石灰的颜色,颜色越白,CaO含量越高。
称量生石灰质量,相同体积生石灰质量越轻,CaO含量越高。
水洗生石灰,水洗后残留量越少,生烧率和过烧率越低,CaO含量越高。
生石灰水化反应越强烈,水温升高越多,生石灰CaO含量越高。
4、生石灰强化烧结过程(生石灰代替石灰石的优点)
详细阐述:
1)亲水胶体作用和凝聚作用,增强料球强度和密度。
2)增加湿容量,减小料球破坏。
3)热稳定性好,保护料球不被破坏。
4)生石灰遇水消化放热,提高混合料温度,减小料层阻力。
5)生石灰消化成消石灰产生H+和OH-是碳素燃烧催化剂,促进烧结料中碳顺利而迅速地燃烧,加快烧结速度,提高烧结生产率。
综上所述,生石灰是铁矿粉烧结必不可少的碱性熔剂,活性度高的生石灰是强化烧结过程的有效途径之一,对烧结提高产量改善质量有显著的正面影响。
5、使用生石灰注意事项
详细阐述
1)生石灰配比适宜
2)生石灰在特定工艺段内完成消化
3)生石灰活性体积适宜
4)生石灰在运输储存过程中避免受潮,防止失去CaO作用和污染环境。
四、白云石、蛇纹石烧结特性和作用
烧结MgO源有白云石、蛇纹石、菱镁石、橄榄石,常用白云石和蛇纹石。
石灰石和石灰石—白云石的过度矿层中也含有2~8%的MgO含量,但烧结配加石灰石是为了提高烧结料CaO含量而不是MgO含量,所以石灰石不是烧结MgO源。
1、详细说明 白云石、蛇纹石的物化特性
2、白云石、蛇纹石的MgO形态和烧结特性
白云石与蛇纹石虽然都属于含MgO源矿物,但因MgO存在形态和矿物性能不同,而且烧结过程中生成的矿物组成不同,对烧结矿产质量影响也不同。
1)随着白云石配比的增加,烧结矿MgO含量从1%提高到2.8%,固体燃耗升高,利用系数降低,转鼓强度呈降低趋势。
详细阐述
2)随着蛇纹石配比的提高,烧结矿MgO含量从1%提高到2.8%,烧结固体燃耗降低,转鼓强度和利用系数提高,烧结矿粒度组成趋于合理,改善冶金性能,转鼓强度呈升高趋势,但蛇纹石配比大于2.5%(因烧结矿碱度和铁矿粉种类不同而不同)后,出现部分柱状和片状结构铁酸钙,转鼓强度不再提高甚至有降低的趋势,还原性也降低。
(1)烧结过程中蛇纹石的热化学性质
3MgO·2SiO2·2H2O吸热2MgO·SiO2+SiO2+2H2O放热2MgO·SiO2+MgO·SiO2
蛇纹石300℃吸热分解出结晶水,685℃生成镁橄榄石2MgO·SiO2和无定性的游离SiO2,813℃镁橄榄石2MgO·SiO2再结晶成为烧结矿中的低熔点粘结相并产生放热效应,且游离SiO2与部分镁橄榄石结合形成MgO·SiO2,有利于MgO的矿化,增加烧结液相量,改善结晶状态和烧结矿转鼓强度。
(2)蛇纹石中MgO属化合态物相,能与Fe2O3和Fe3O4构成铁矿物粘结相,而不破坏烧结矿转鼓强度,镁橄榄石2MgO·SiO2即使不与其它矿物反应也能起粘结相作用,无需经过固液相反应,固体燃耗较白云石低,如果蛇纹石粒度细,降低燃耗效果更明显。
(3)蛇纹石中结晶水分解改善烧结过程均匀矿化,烧结料层中氧位升高,增加铁酸钙生成量,而且再结晶后的镁橄榄石2MgO·SiO2在烧结温度下难以熔化起骨架的作用,有利于转鼓强度、利用系数和成品率的提高。
(4)蛇纹石主要组成为MgO和SiO2,配加蛇纹石不仅带入活性较高的MgO,使之易与其它组分形成化合物,改善MgO反应活性,同时提高烧结矿中SiO2含量,高铁低硅烧结条件下提高烧结矿产质量指标。
(5)蛇纹石熔剂的粘结相强度高
以上综述是蛇纹石优于白云石的根本原因。蛇纹石粒度细(小于2mm)能更好发挥其烧结特性,利于增强烧结过程氧化性气氛并改善热态透气性,促进生成铁酸钙,利于蛇纹石的矿化,为提高成品率和转鼓强度、改善低温还原粉化性能创造有利条件。
随着蛇纹石配比的增加,控制烧结矿Al2O3含量在1.0~1.8%不宜过高,Al2O3/SiO2在0.1~0.35不超过0.4,否则铝固熔于铝硅铁酸钙SFCA增多,会部分结合烧结矿中的CaO和SiO2,减少CaO和SiO2参与形成的粘结相,降低烧结矿转鼓强度,因此在考虑降低Al2O3/SiO2的同时,增加CaO含量生产高碱度烧结矿,促进生成铁酸钙而减少赤铁矿含量,同时实施低温烧结生成针状铁酸钙,对于改善烧结矿转鼓强度和还原性具有重要意义。
3)蛇纹石改善烧结矿还原性
烧结过程中蛇纹石分解出结晶水,促进蛇纹石均匀矿化,固体燃料用量一定情况下烧结料层氧位提高,随着蛇纹石配比的提高,烧结矿FeO含量降低,还原性好。
蛇纹石中的镁橄榄石2MgO·SiO2晶体不但提高转鼓强度和软化温度,同时改善还原性能,因为还原过程中镁橄榄石受热产生异轴膨胀,有利于还原气体的扩散。
配加白云石,烧结矿粘结相中玻璃质和MgO均属均质体和等轴晶系,受热后产生等向膨胀,造成的间隙不大或没有,不利于还原。
3、烧结料中MgO的作用和影响
详细阐述
1)MgO改善烧结矿低温还原粉化性能
2)MgO改善烧结矿软熔性能
3)MgO对转鼓强度和还原性有正负双重影响
4)MgO降低烧结生产率
五、改进固体燃料加工流程
固体燃料水分大时,极易堵塞筛孔,筛分效率低且影响正常生产,不宜采用闭路预先筛分破碎流程。
固体燃料水分小于10%且粒度小(-10mm,其中-3mm粒级占50%以上)时,采用闭路预先筛分(考虑到焦粉易堵塞筛孔和提高筛分效率,选用4mm预筛分)一段破碎工艺流程,筛下物直接进配料室燃料仓参与配料,筛上物进四辊细碎,既减少燃料过粉碎现象,改善燃料加工粒度,又降低燃料加工成本。
弛张筛预筛分固体燃料效果良好,弛张筛筛网交替拉紧和松弛的弛张运动,增加筛面振动幅度,使固体燃料产生前进弹跳运动,有效克服了固体燃料黏附筛网和筛孔堵塞现象,筛分效率高,动负荷小,功耗小,噪声低。
柔性聚氨酯筛适用于筛分细、黏、湿、腐蚀性的物料,如焦粉、焦炭、黏性大水分大的块矿等,柔性筛网蹦床式上下做功,物料呈翻滚跳跃式前行,有效解决筛网糊堵现象,筛分效率高,具有耐磨性,寿命长,筛分过程污染小噪音小。
六、快速调整烧结矿碱度方法
烧结过程与配料计算过程对照表
烧结过程 配料计算过程 | |||
烧结 机头 | 物理水分蒸发(成为干基烧结料) | 烧结机尾 | |
结晶水分解、碳酸盐分解、铁氧化物氧化还原、脱硫脱硝等(烧损) | |||
湿配比 | ∑湿配比×(1-水分)=∑干配比 | 烧结饼 | 成品烧结矿+内返 |
∑干配比×(1-烧损)=残存δ | 铺底料 | ||
物料CaO | CaO烧结料=∑物料湿配比×(1-水分)×CaO物料 | CaO烧结矿=CaO烧结料÷残存量 | |
物料SiO2 | SiO2烧结料=∑物料湿配比×(1-水分)×SiO2 | SiO2烧结矿=SiO2烧结料÷残存量 | |
… | ……… | ……… | |
出矿率 | 出矿率=(烧结饼÷干基烧结料量)×100% | ||
烧成率 | 烧成率=(成品烧结矿量÷干基烧结料量)×100% | ||
成品率 内返率 | 成品率=(成品烧结矿量÷烧结饼)×100% | ||
内返率=(内返量÷烧结饼)×100% | |||
成品率+内返率=100% |
由此推导出:烧结矿碱度R=烧结料碱度R
通过分析烧结料碱度就可得知烧结矿碱度是否合格,但需注意当烧结料中没有固体燃料时,化验分析烧结料碱度结果较准确,在允许误差范围内,而且不损坏熔样铂金坩埚。如果烧结料中有固体燃料,在化验分析前焙烧烧结料的温度和氧化还原气氛(烧损和残存程度)与烧结生产实际相差较大,影响分析结果不准确。
当烧结矿碱度出现废品时,在配料室取调整碱度后的新原料配比(固体燃料除外),将取样充分混匀后分析CaO和SiO2含量,可快速得知调整碱度情况,减少碱度废品批次。
七、概念:烧结饼、烧成率、成品率、内返率、矿耗
烧结机机尾烧结饼落下后,过程损耗忽略不计,经过破碎筛分整粒,分为成品烧结矿和烧结内返量(视铺底料恒定不变),即烧结饼=成品烧结矿量+内返量。
烧成率指干基烧结料灼烧成烧结饼后经破碎筛分整粒产生成品烧结矿的百分数。
烧成率与烧结物料的烧损有关,同时与生产操作好坏有很大关系。
成品率指烧结饼经破碎筛分整粒产生成品烧结矿的百分数。
内返率指烧结饼经破碎筛分整粒产生内返量的百分数。
矿耗指生产1吨成品烧结矿所需干基烧结料吨数,矿耗=0.01干配比÷残存,单位t/t。
混合机混匀制粒时间、填充率、规范转速、混烧比的计算
混合机内加水点和加水部位的布置
八、处理料仓粘料方法和使用效果
1、在仓壁下部两侧安装电振器、声波振动器、空气炮,粘料严重时启动振打。
使用效果:因为是在料仓外部局部阶段性振打,处理粘料有限,运行一段时间需要人工清料。
2、在料仓内部侧壁上悬挂衬板,通过振打衬板清理粘料。
使用效果:虽然清料设施装在仓内,但因悬挂衬板处于静态,其上面很容易粘料而且难以振打下去,料仓粘料问题仍然得不到解决。
以上是烧结处理料仓粘料常用的方法,但仅能局部、十分有限地处理粘料,每隔40天左右粘料越来越多且密实难处理,需要人工清理,不仅影响停机,而且作业空间狭窄,存在很大的安全隐患。
3、在料仓内壁四周安装液压自动清料铲,能够大面积直接破坏粘料而不积料,疏通清理料仓粘料效果好,无需人工清料,从根本上解决料仓粘料的问题。
九、铺底料粒级和厚度
保证铺底料不堵塞炉条间隙(一般7~9mm为宜)的情况下,铺底料粒级宜小而均匀10~16mm,厚度以30~40mm为宜。其好处有:
1)均匀气流分布,改善滤层作用,易控烧结终点。
2)改善成品烧结矿粒度组成,提高转鼓强度和产量。
以360m2烧结机2.3m/min机速,烧结矿堆比重1.65t/m3测算,铺底料每降低10mm,增产218.6吨/日。
某厂测定同一批烧结矿,成品烧结矿转鼓强度79.7%,10~20mm铺底料转鼓82%。
某厂测定不同粒级烧结矿转鼓强度
粒级mm | 10~16 | 16~25 | 25~40 | +40 |
转鼓强度% | 75.37 | 75.56 | 74.48 | 74.31 |
十、低负压点火措施和好处
1、低负压点火的主要措施
1)点火风箱负压独立控制,提高点火风箱严密性。
2)点火风箱隔板采用柔性中部密封,与台车底梁更贴合。
3)改进点火风箱支管内积料排放方式,彻底解决因卡料堵料而加大支管蝶阀开度造成点火风箱负压高的问题。
4)控制炉膛静压在-50Pa以下,点火风箱负压-8KPa以下的良好效果。
5)稳定料层厚度是基础,稳定烧结料水分是前提。
6)变更原料结构,烧结料过于松散、料层透气性过剩时,适当压下烧结料层。
7)控制适宜点火空燃比和点火强度,防止火焰外扑或内收。
2、低负压点火的好处
1)阻止外界冷空气吸入炉膛,降低点火煤气单耗。
2)改善台车边部点火效果,延长表层高温保持时间,提高成品率,降低燃耗。
3)保持原始料层透气性而不被破坏,增加通过料层有效风量,加快垂直烧结速度,提高成品烧结矿产量。
4)减少点火带入料层的NOx含量。
十一、高碱度烧结矿的特点
通常将碱度R1.8~2.2的烧结矿称为高碱度烧结矿,碱度R>2.2的烧结矿称为超高碱度烧结矿。
详细阐述
1、高碱度烧结矿的转鼓强度、还原性、低温还原粉化性都好
2、高碱度烧结矿荷重还原软化性和熔滴性能好
3、高碱度烧结矿生产率高
4、高碱度烧结矿影响脱硫率降低
5、生产高碱度烧结矿注意事项
1)碱度R<2.2为宜
2)适宜低负压生产
3)原料粒度适当小一些
4)适宜SiO2含量和配碳量
5)选用低硫低硅的原燃料,以满足脱硫和堆密度的要求。
十二、铁酸钙固结理论
在低配碳量和低温烧结条件下生产高碱度烧结矿,烧结料中CaO和Fe2O3首先发生固相反应进而熔融形成液相,生成强度高、还原性好的针状铁酸钙粘结相,并以此来粘结包裹未起反应的残存未熔矿粉,进一步生成针状铝硅铁酸钙SFCA的烧结机理,称为铁酸钙固结理论。
SFCA烧结矿中,有80%的SiO2进入SFCA,降低难还原的硅酸盐液相,大幅度降低强度差的硅酸二钙C2S数量,且因大量Fe2O3形成针状结构SFCA,减少再生骸晶状Fe2O3,改善低温还原粉化性。
铁酸钙固结理论的必要条件:
1、高碱度
虽固相反应中铁酸一钙生成早生成速度快,但一旦形成熔体后,熔体中CaO和SiO2的亲和力、SiO2和FeO的亲和力都比CaO和Fe2O3亲和力大得多,因此最初生成的铁酸一钙CF容易分解形成CaO·SiO2熔体,只有当CaO过剩(即高碱度)时,CaO才能与Fe2O3作用生成铁酸一钙。
碱度低时不仅SFCA少,且铁酸钙大多为片状和柱状。碱度R>2.2又出现大量难还原铁酸二钙2CaO·Fe2O3。适宜碱度R1.9~2.15,最低不低于1.85,最高不超过2.2。
2、低温烧结
烧结温度1100~1200℃时铁酸钙晶体间尚未连接,烧结矿强度差。
烧结温度1200~1250℃时铁酸钙晶桥连接,有针状交织结构出现,强度较好。
烧结温度1250~1280℃时,铁酸钙呈交织结构,强度最好。
烧结温度低于1280℃,高温持续时间长,十分有利于针状铁酸钙形成和发育。
烧结温度高于1280℃,SFCA开始分解,铁酸一钙数量减少,且由针状转变为柱状铁酸钙,强度上升但还原性下降,且温度高易产生大量NO和致癌物质二噁英。
适宜烧结温度1230~1280℃,磁铁精矿粉烧结取低值,赤铁矿粉烧结取高值。
3、强氧化性气氛
强氧化性气氛下,以磁铁精矿粉为主料进行烧结,促进Fe3O4氧化成Fe2O3,有利于生成铁酸钙;以赤铁矿粉为主料进行烧结,阻止Fe2O3还原为Fe3O4,减少FeO含量,减少铁橄榄石液相生成量,使铁酸钙液相起主要粘结相作用。
4、适宜铝硅比Al2O3/SiO2
烧结料SiO2和Al2O3含量对生成SFCA有重要影响。研究表明SiO2含量很低时只能生成片状铁酸钙,SiO2达3%时SFCA开始由片状向针状发展,SiO2为4~8%时获得针状交织结构的SFCA,但SiO2含量高时还原性差,特别是1200℃高温还原性差。烧结矿Al2O3/SiO2在0.1~0.35不超过0.4时,促进生成SFCA。
5、保温
烧结料宜在1100℃以上温度区保持6min,有利于生产SFCA烧结矿。
十三、有效风量对产质量和电耗的影响
烧结过程传热机理表明,尽管原料品种、原料配比、配碳量不同,但吨烧结料所需风量相近,一般设计取烧结机有效面积抽风量90~95m3(工况)/m2·min。
其它条件一定时,烧结有效风量与总管负压、垂直烧结速度、电耗的关系式如下:
(1)△P=K1V1.8 (2)υ⊥=K2V0.9 (3)Q=K3V1.9
式中V——烧结有效风量,m3/min
△P——总管负压,Pa
υ⊥——垂直烧结速度,mm/min
Q——烧结矿电耗,KWh/t
K1、K2、K3——与原料性质和操作有关的系数
风是烧结过程赖以进行的基本条件之一,也是加快烧结过程最活跃的因素,关系式(1)表明,通过料层的有效风量越大,垂直烧结速度越快,提高烧结生产率,一定范围内有效风量与烧结矿产量成正比,但当垂直烧结速度增大到一定程度后,继续增加风量,则因垂直烧结速度过快,表层烧结矿冷却加剧,燃烧带固结成型条件差,烧结矿转鼓强度将有一定程度的降低,抵消了生产率增长的优势且烧结矿质量变差。
关系式(2)和(3)表明,有效风量增加,总管负压和电耗基本呈平方关系明显增加,增长幅度远远大于垂直烧结速度,影响烧结产能降低能耗升高,同时大风量高负压下,漏风率增大,烧结矿气孔率减小,还原性下降。
大风量高负压操作不是理想的烧结方法,生产中要根据原料条件、料层厚度、烧结料水碳、产质量和能耗指标等综合因素,控制适宜有效风量合理用风。
烧结生产中,不能单纯强调提高烧结风量,而应当强调提高烧结有效风量,因为只有通过料层的有效风量才能为烧结料中的碳燃烧提供氧量,所以在抽风能力一定条件下,应当努力减少有害漏风量,提高有效风量,加速料层垂直烧结速度。
对于抽风系统,降低漏风率,提高烧结有效风量,则充分利用主抽风机能力。
通过提高主抽风机能力增加有效风量,会带来电耗和漏风率升高的负面影响。如果烧结机抽风系统漏风严重,尽管提高主抽风机能力,烧结有效风量也增加很少,因此积极减少有害漏风,提高有效风量很重要。
改善烧结过程料层透气性是增加有效风量极力提倡的措施,有利于提高料层厚度,实施大风量低负压烧结,提高转鼓强度,降低燃耗,降低FeO含量和烧结返矿率。
十四、烧结机风、水、碳、烧结终点操作要点
详细阐述
1、烧结机合理用风
2、目测判断烧结料水分
3、控制烧结固体燃耗
1)烧结三碳基本要求
2)烧结固体燃料操作要点
烧结料固定碳主要由固体燃料带入,高炉炉尘、烧结内返等含碳物料带入少部分。
(1)影响固体燃料用量的因素
(2)固体燃料用量判断
固体燃料用量直接影响燃烧带温度和厚度、垂直烧结速度、烧结气氛、烧结矿转鼓强度和还原性等。
详细说明:固体燃料用量大或小时,烧结机、烧结过程、烧结矿质量的表象。
3)详细阐述固体燃料粒度要求及其影响
(1)固体燃料粒度过粗的影响
(2)固体燃料粒度过细的影响
4)降低烧结固体燃耗的主要措施
(1)提高料温增加烧结料带入的物理热,减少废气带走热量,实施环冷机余热回收利用等。
(2)增加氧化放热原料,减少吸热原料。
(3)充分利用固体燃料的燃烧热
(4)提高成品率
采取多种有效措施,如加强原料中和混匀、返矿平衡、稳定烧结料水碳操作、减少漏风提高有效风量、抑制边部效应、微负压点火、低负压烧结、稳定控制烧结终点等,改善烧结矿质量,提高成品率,降低内返率。
(5)改进工艺技术
强力混合机混匀和强化制粒,实施厚料层低水低碳烧结,降低上层烧结矿比例,增加料层自动蓄热所提供的热量。料层厚度+100mm,燃耗-1~2Kg/t。
高碱度低温烧结,提高烧结过程氧位,控制烧结料中Al2O3/SiO2在0.1~0.35,改变粘结相的生成条件,减少硅酸盐粘结相,充分发展以铝硅铁酸钙系粘结相和原生赤铁矿为主的非均相烧结矿,降低烧结矿FeO含量,提高软化和熔化温度,改善软熔性。
4、烧结终点操作要点
烧结三点温度指点火温度、终点温度、总管废气温度。
终点温度指烧结到达终点位置风箱处的温度,整个料层高度均为烧结矿带,终点温度反映燃烧带温度(即烧结温度)的高低。
总管废气温度指各风箱集气管中的温度,即烟道温度,一般在进入机头电除尘器之前安装热电偶测定。
详细说明:
1)判断烧结终点
2)控制烧结终点
3)烧结终点对烧结矿产质量的意义
十五、影响烧结矿FeO含量的因素
详细阐述
1、原始烧结料氧化度和宏观烧结气氛指数影响FeO含量
2、工艺操作制度影响FeO含量
3、烧结矿碱度、SiO2和MgO含量影响FeO含量
4、烧结料层厚度影响FeO含量
十六、褐铁矿粉烧结技术
详细阐述
1、提高烧结料水分
2、降低点火温度,提高保温炉热量投入。
3、固体燃料配比适宜
4、慢烧过程控制
5、优化配矿发挥褐铁矿烧结特性
十七、影响烧结矿转鼓强度的因素
详细说明
1、铁矿粉的种类和烧结特性
2、固体燃料和熔剂质量
3、返矿的质量和数量
4、烧结矿的碱度和矿物组成
5、烧结矿SiO2和FeO含量、MgO和Al2O3含量
6、主要操作参数:料层厚度、水分、配碳量、布料点火、烧结速度和冷却速度
十八、烧结矿低温还原粉化的根本原因和影响因素
1、烧结矿低温还原粉化的根本原因
高炉低温还原区下,一方面烧结矿中Fe2O3极易被还原成Fe3O4,还原过程中体积膨胀,产生极大内应力,释放应力加剧裂纹扩展而引起粉化。另一方面烧结矿中再生骸晶状赤铁矿由α—Fe2O3转变为γ—Fe2O3晶格转变造成结构扭曲,产生极大内应力,烧结矿强度遭到破坏,抵御还原粉化的能力差,在挤压碰撞作用下烧结矿碎裂粉化。
烧结矿逐级还原过程中体积变化如下:
Fe2O3——Fe3O4——FeO——Fe
体积100 125 132 127
烧结矿是多种矿物的集合体,冷却过程中由于不同矿物的冷缩系数不同而产生应力,往往在烧结矿中强度较低的部位产生裂纹。温度较低时,烧结矿性脆,还原过程产生的内应力引起应变,烧结矿耐不住这种应变产生新的裂纹,并使原有的裂纹扩张,致使烧结矿粉碎。
2、影响烧结矿低温还原粉化的因素
1)铁矿石种类和Fe2O3结晶形态
2)烧结工艺条件
3)烧结矿碱度
4)烧结矿中脉石成分
5)还原温度和还原时间
购买热线:0311-85395669
:13303214617/15373055160
部分目录
第一部分烧结原料基础知识
四大类铁矿粉的烧结特性
提高混匀效果的主要措施
生石灰主要特性和作用
白云石、蛇纹石烧结特性和作用
焦粉和无烟煤烧结性能比较
改进固体燃料加工工艺流程
第二部分烧结配料理论和技能
调整烧结矿碱度配料计算
快速调整烧结矿碱度方法
影响配料准确性的主要因素
第三部分烧结混匀制粒理论和技能
混合机工艺参数计算及其对混匀制粒的影响
影响混匀制粒效果的主要因素
提高烧结料温度的主要措施
第四部分布料点火烧结理论和技能
烧结机布料装置及改进
常用的处理粘料方法和使用效果
烧结机边部效应测定方法和抑制措施
点火参数控制及其对烧结过程的影响
微负压点火的主要措施
判断过湿带消失和减轻过湿带的主要措施
烧结料层结构及改善烧结料层透气性主要途径
固相反应的机理、特点、作用、影响因素
烧结料化学成分影响烧结矿矿物组成
高碱度烧结矿的特点和生产注意事项
铁酸钙固结理论的必要条件
操作工艺制度影响烧结矿矿物组成和结构
烧结矿的矿物组成和结构对转鼓强度的影响
烧结操作方针
影响废气温度的因素
烧结漏风率测定方法和计算
烧结机风、水、碳、烧结终点操作要点
影响烧结矿FeO含量的因素
烧结矿FeO含量对质量的影响
降低烧结矿FeO含量的主要措施
铁矿粉烧结基础特性含义、测定、影响因素、配矿原则
褐铁矿粉烧结技术
第六部分烧结技术进步
厚料层烧结技术问题
厚料层烧结的工艺技术措施
低温烧结生产措施
低硅烧结工艺条件
第七部分烧结主要技术经济指标
影响烧结矿转鼓强度的因素
影响烧结矿还原性的因素
烧结矿低温还原粉化的根本原因和影响因素
第九部分烧结烟气污染物治理
烧结过程NOx 生成影响因素
烧结烟气脱硫脱硝工艺技术
烧结烟气二噁英治理
烧结烟气拖尾减白技术
《现代烧结生产实用技术》一书从烧结原料、烧结矿质量到烧结烟气污染物治理共分九部分的内容,突出“现代烧结”和“实用技术”,起到指导日常工作的作用,值得阅读学习。
该书25万余字,取材新颖,适应现代烧结生产技术发展的需要,内容涵盖较详尽,问题阐述较深刻,贴近生产实际,专业性和实用性强,具有推广意义,是烧结行业工作者可选且不可多得的科技用书。
作为烧结岗位和专业技术人员查阅用书,更适合烧结技术比武理论实操学习和试题资料用书,内容以问答的形式简捷明了,语言精炼易懂,有助于学者弄清模糊概念,发现认知误区,提高学习效果。
购买热线:0311-85395669
:17330092395/13303214617
购买热线:0311-85395669
:13303214617/15373055160
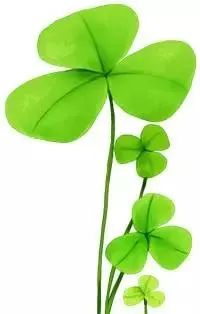
优秀供应商推荐
专注轧钢加热炉、炼铁热风炉脱硫、脱硝工程—北京赛博宇科技发展有限公司
粉尘检测监测仪
环保设备专家——河北远芳环保设备有限公司
VPSA变压吸附制氧装置专家——湖北中船气体有限公司
新技术--冶金固废资源化利用专利12项
变压吸附技术领航者——昆山锦程气体设备有限公司
河南凯博机械烘烤产品介绍
均流式电除尘技术——北京力博明科技发展有限公司
铁水运输全程加盖保温技术——无锡市力成液压机械有限公司
国家铁包盖行业标准制定者——南通市煌埔机械
昊康江苏气力输送成套设备有限公司
钢铁行业热成像系统总汇—常州荣邦
相关资源